
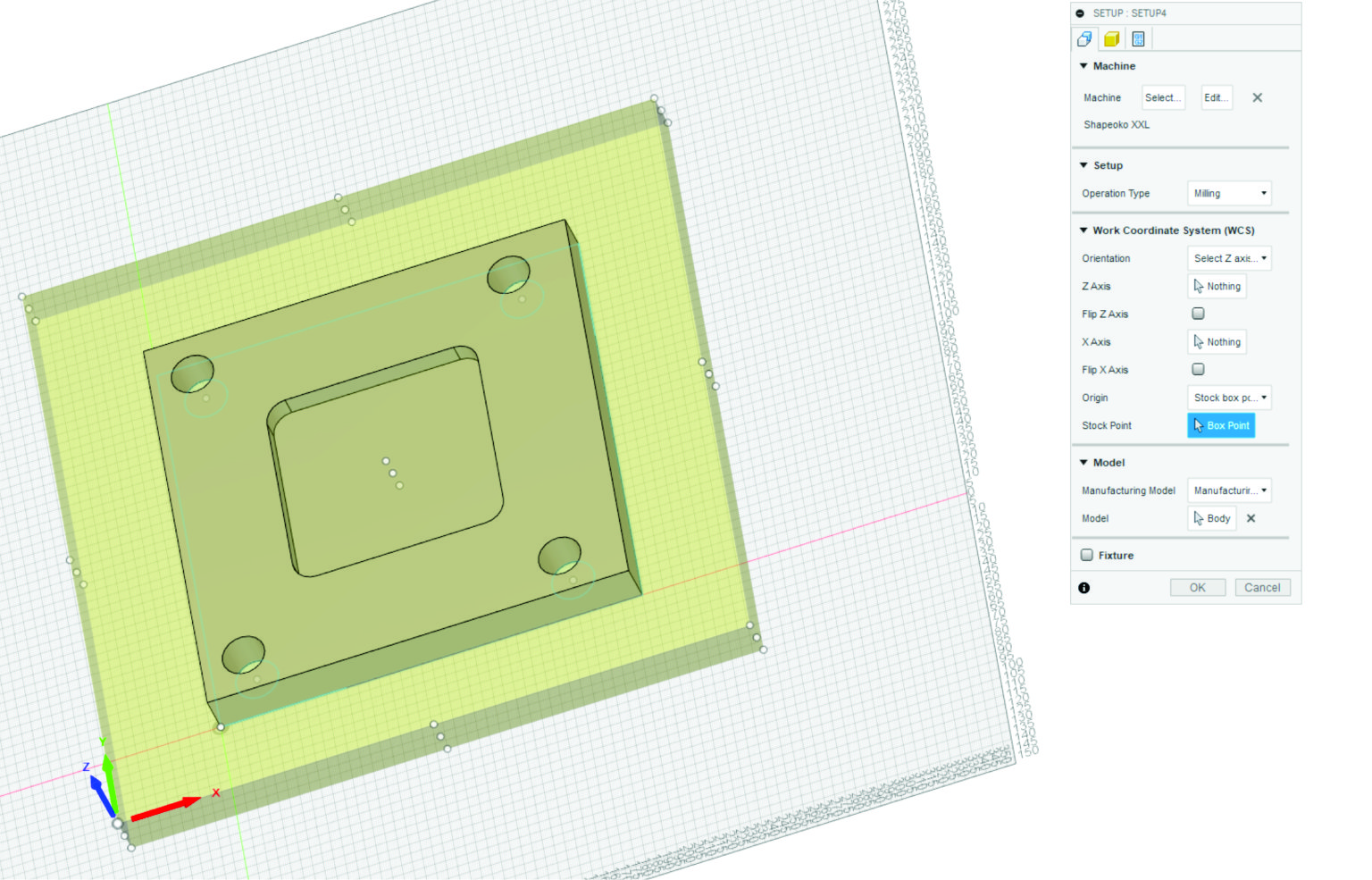
That being said, under info panel I see that this data exists and the form of dimensions being 0 for the machine. For some reason under my Machine definition settings I am missing the Dimensions and Workpiece settings.
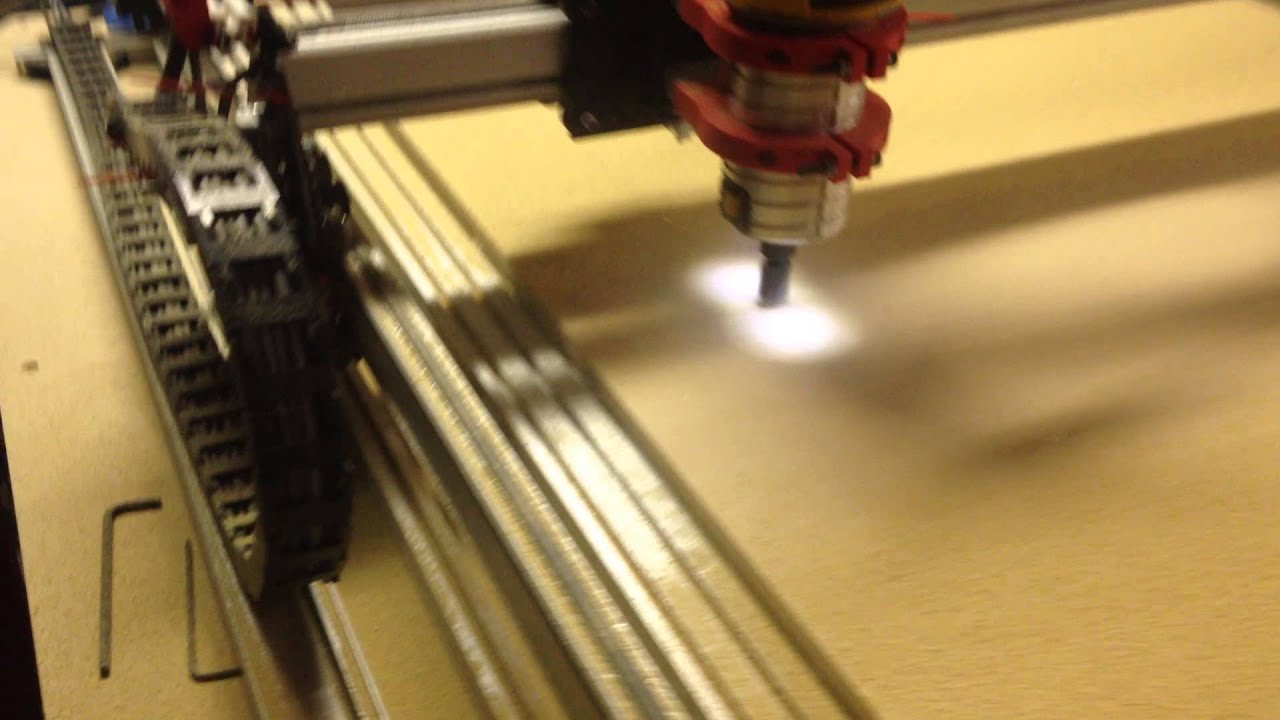
I am still refining it, but as of now it works perfectly. Defining machine in Fusion 360 I am new and trying to define Shapeoko 5 pro in fusion. It works with a range of hose diameters for maximum compatibility with your vacuum: 2.5 Direct hose. My DIY version of the Shapeoko Bitsetter Hey everyone, I have been learning fusion 360 for a few months now and wanted to try my hand at making something a little more complicated (for me). Ive also attached my Fusion360 file so you can follow along as I walk through the design and CAM process. I've attached the fusion 360 file as well as the resulting gcode. Shapeoko includes our Sweepy V2 dust boot to help keep your Shapeoko CNC router, and your shop, as clean as possible. Ive found that it works great with the Shapeoko 3. It seems like I need to tell the machine to use the CNC probed position as the material start position but I'm unsure how to do so, or why that wouldn't be handled by post processing with the carbide3D config. good introduction to more complex projects, and the Fusion 360 CAM workspace. I've tried moving the component to origin in fusion, selecting the material body under the Manufacture Setup for the toolpaths, nothing seems to work. For those completely new to CNC routing, the official Shapeoko Hello World. Shapeoko 4 comes in 3 sizes: Standard (17.5 x 17.5), XL (33 x 17.5), XXL (33 x 33). Current versions of Fusion 360 from Autodesk have a built-in post-processor for Carbide 3D machines. When creating the gcode through fusion I used the default Carbide3D config, I've also tried a user posted ShapeOKO config and have the same issue. Shapeoko Pro is a CNC router that can run all day long. Using Fusion 360 with Carbide 3D machines. 35 Free Helical Gear Generator Easily create Helical, Double Helix, Herringbone, and Spur Gears, with or without backlash, using the Metric system of gear specification. The issue I'm running into is the CNC is not starting at the home position I set using the xyz touch probe, but rather moving to the front most extent on the Y- axis and beginning to cut where there is no material. An Autodesk Fusion 360 add-in for creating Spur, Internal and Rack gears. I created a design using Fusion 360, generated the gcode and I'm using Carbide Motion as the gcode sender. Print settings: PLA or PETG 0.25mm layer.
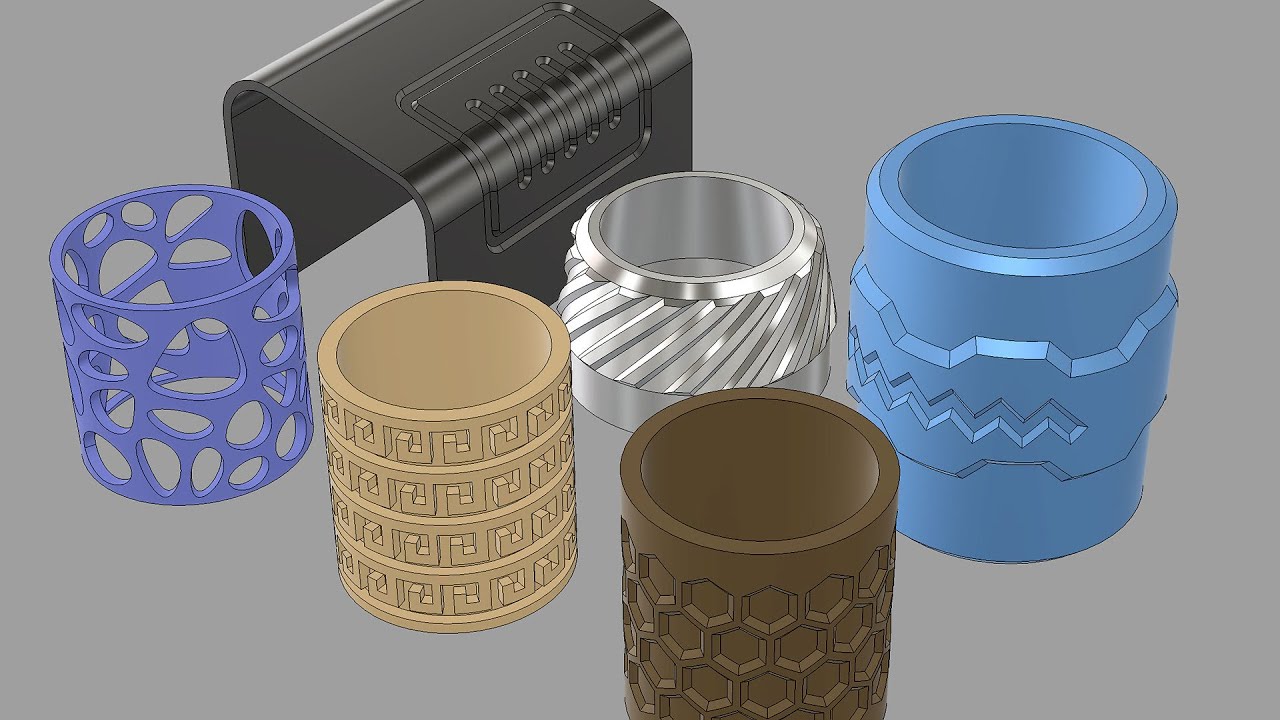
Copyright (C) 2012-2022 by Autodesk, Inc.Ĭarbide 3D Grbl post processor configuration.I'm very new to Fusion 360 and the Shapeoko CNC and am attempting my first 3d project. STL and Fusion 360 files have been added for the Short version.
